Advancing Modular Construction through 3D Printing: Opportunities in Precision and Efficiency
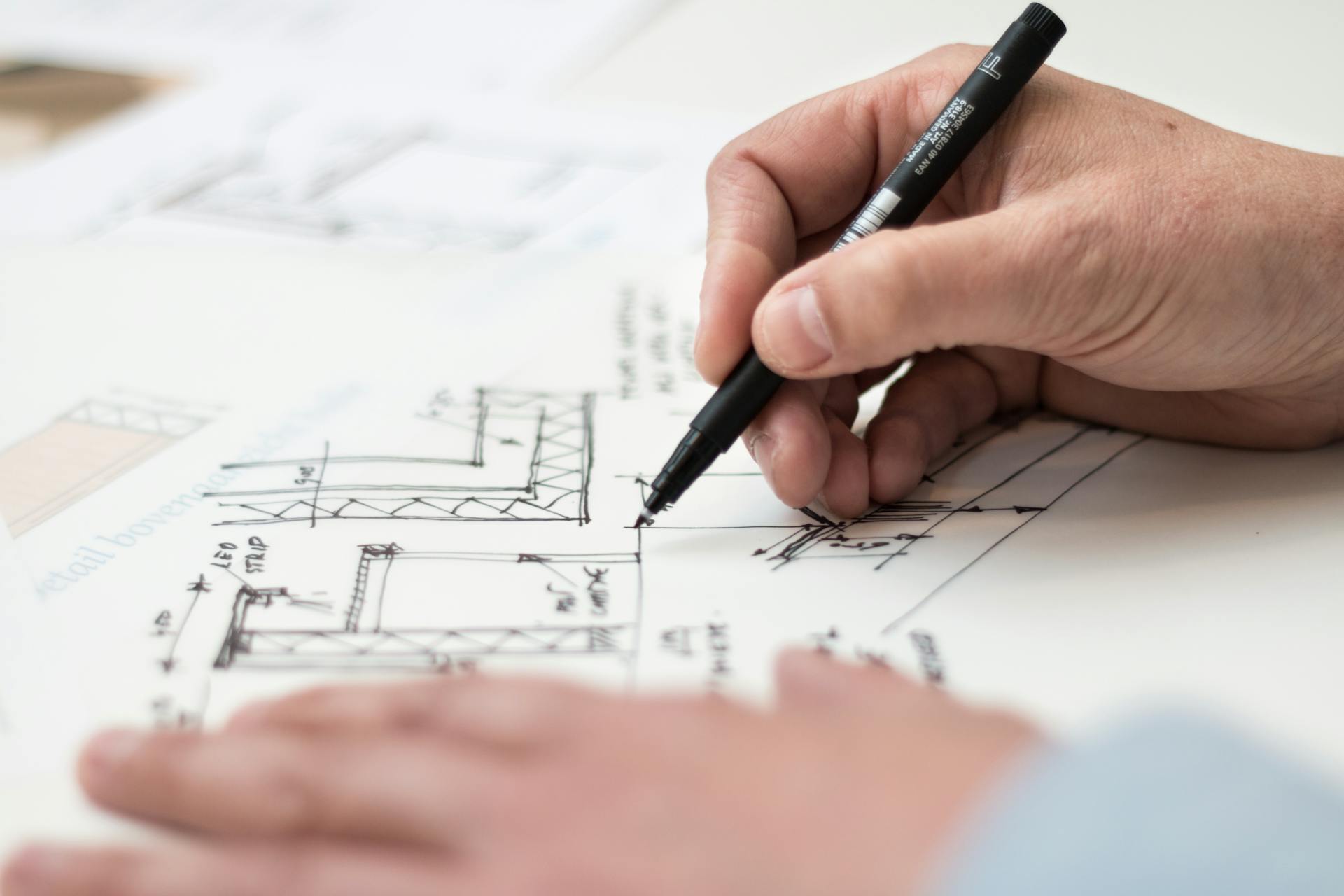
Modular construction has gained significant traction as an innovative approach to building design and assembly. By delivering pre-fabricated components to construction sites, this method streamlines operations, cuts timelines, and improves consistency. Now, the integration of 3D printing technology is poised to elevate modular construction to new heights, offering game-changing solutions in precision, efficiency, and sustainability. This blog explores the transformational benefits of 3D printing in modular construction, its current challenges, and the future outlook for this cutting-edge synergy.
1. Benefits of 3D Printing in Modular Construction
1.1 Enhanced Precision
3D printing employs advanced CAD models and automated processes that ensure a higher degree of dimensional accuracy. This minimizes errors and rework commonly associated with traditional construction—critical when modules must fit together seamlessly on-site.
1.2 Accelerated Construction Timelines
By producing components on-demand with automated printers, 3D printing simplifies and expedites workflows. Faster lead times—especially for repetitive or complex parts—allow developers to meet tight schedules without compromising quality.
1.3 Cost Efficiency
Eliminating large-scale molds, formwork, and certain manual labor tasks translates into significant cost savings. Material waste is minimized by depositing only what’s needed, and labor-intensive processes become automated, boosting profitability for modular firms.
1.4 Customization & Design Flexibility
Unlike traditional prefab methods, 3D printing enables architects to experiment with intricate geometries and non-standard shapes at little extra cost. This unlocks unique building aesthetics and functional designs without lengthy tooling changes.
1.5 Reduced Waste & Environmental Impact
As sustainability becomes paramount, 3D printing’s ability to minimize raw-material waste is a major advantage. Paired with modular construction’s inherent efficiency, these technologies drive greener practices by lowering embodied carbon and site disturbance.
2. Challenges & Considerations
- High Initial Investment
Industrial-grade 3D printers and skilled operators require significant up-front capital, posing a barrier for smaller firms. - Material Limitations
While concrete and thermoplastic composites are advancing, the range of approved, certified materials remains narrower than traditional options. - Regulatory & Code Compliance
Building codes and structural standards must evolve to address novel printed components, which can delay approvals. - Industry Adoption Curve
Conservative procurement practices and familiarity with conventional methods can slow integration of emerging technologies.
3. Future Trends in 3D Printing for Modular Construction
- Advanced Materials
Innovations such as carbon-reinforced concrete, geopolymer mixes, and bio-based polymers will expand printing applications and performance. - AI-Driven Design Optimization
Generative algorithms will automatically refine module geometries for maximum strength, minimal material use, and aesthetic appeal. - Robotic Integration
Fully automated printing arms and gantry systems on-site will combine assembly and printing in one continuous workflow. - Regulatory Evolution
As case studies accumulate, standards bodies will codify guidelines for printed modular components—accelerating mainstream uptake.
4. Driving Precision and Sustainability in Construction
The fusion of 3D printing with modular construction represents a paradigm shift with the potential to redefine the industry. By improving dimensional accuracy, accelerating schedules, lowering costs, and fostering sustainability, this synergy unlocks remarkable opportunities for developers, engineers, and architects. Overcoming initial investment and regulatory hurdles will be key—but the rewards are transformative.
For firms eager to stay ahead, now is the time to explore how 3D printing can integrate into your next modular project. Invest in pilot programs, partner with technology providers, and begin planning for a future where precision and sustainability go hand in hand.