Mitigating Support Loss from Machinery-Induced Vibrations: Structural Impacts and Engineering Solutions
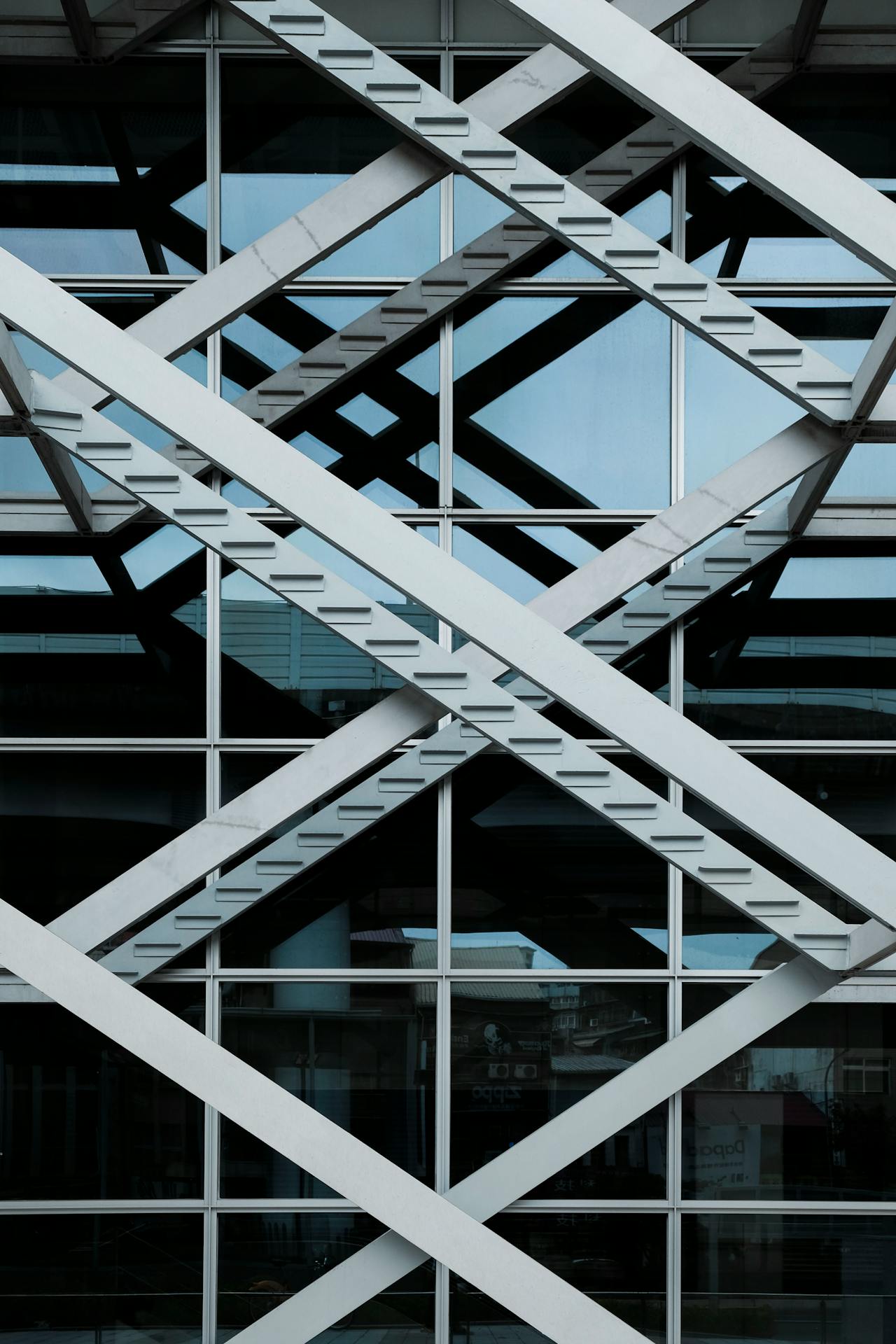
Machinery-induced vibrations are a persistent challenge in industrial and mechanical engineering. Caused by factors such as imbalances or misalignment within machinery, these vibrations pose significant risks to structural integrity and support systems. Over time, unchecked oscillations can degrade foundations, misalign components, and lead to costly downtimes or structural damage. This article explores the origins of machinery-induced vibrations, their impact on structural supports, and effective engineering solutions for mitigation.
1. Understanding Machinery-Induced Vibrations
1.1 Sources of Vibrations
- Imbalances in rotating components that generate uneven centrifugal forces.
- Misalignments of shafts or bearings, producing oscillatory motion.
- Wear and Tear in gears, couplings, or other moving parts, amplifying noise and vibration.
- External Influences such as adjacent equipment operation or environmental forces (e.g., wind, seismic activity).
1.2 Propagation of Vibrational Energy
Mechanical vibrations travel through structures like waves, transferring energy to neighboring components, floors, and foundations. Weak or inadequately supported areas can amplify these effects.
1.3 The Role of Resonance
When machinery vibration frequencies match a structure’s natural frequency, resonance occurs—dramatically increasing amplitude and accelerating fatigue in both the equipment and its supports.
2. Impact on Structural Supports
Machinery-induced vibrations can have serious consequences:
- Bearing Wear: Excessive oscillations lead to premature bearing failure.
- Foundation Damage: Repeated vibrational forces cause cracking, settlement, or loosening.
- Support Weakening: Long-term exposure degrades beams, frames, and anchor bolts, threatening stability.
Routine inspections and vibration monitoring are vital to detect vulnerabilities early and extend the life of both machinery and its support structures.
3. Engineering Solutions for Vibration Mitigation
3.1 Vibration Isolation
- Rubber Mounts & Spring Isolators: Absorb and attenuate transmitted vibrations.
- Floating Floors: Decouple machinery from the base structure to prevent energy transfer.
3.2 Damping Methods
- Viscoelastic Dampers: Convert vibrational energy into heat, reducing amplitude.
- Tuned Mass Dampers: Introduce a counter-oscillating mass to neutralize dominant frequencies.
3.3 Structural Modifications
- Precision Balancing & Alignment: Minimize inherent imbalance and misalignment at the source.
- Stiffening & Retrofitting: Increase support rigidity or adjust natural frequencies to avoid resonance.
By combining isolation, damping, and targeted structural upgrades, engineers can dramatically reduce harmful vibrations and improve overall system reliability.
4. The Case for Proactive Vibration Management
Investing in comprehensive vibration control—including diagnostics, continuous monitoring, and advanced mitigation techniques—yields tangible benefits:
- Enhanced Equipment Longevity
- Reduced Maintenance Costs
- Improved Safety & Uptime
Emerging technologies such as AI-driven vibration analysis and adaptive damping systems promise even greater precision and scalability. Organizations that adopt these proactive strategies will safeguard their assets and maintain a competitive edge in tomorrow’s industrial landscape.
Takeaway:
Proactively addressing machinery-induced vibrations through a blend of engineering best practices and innovative technologies is essential for preserving structural integrity, minimizing downtime, and ensuring safe, efficient operations.